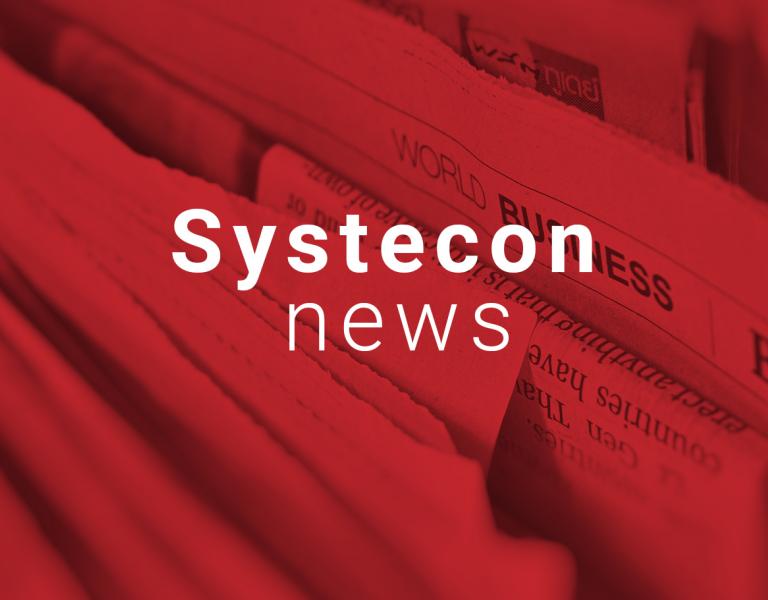
BAE Systems - LCC analysis provides decision support for design changes
Life Cycle Cost (LCC) analyses shouldn’t only be performed prior to or during the acquisition phase of a system or a product, but also continuously throughout the system’s life cycle. Systecon's analysis of the more than 20-year-old Combat Vehicle 90 is a good example of that.
Life Cycle Cost (LCC) analyses shouldn’t only be performed prior to or during the acquisition phase of a system or a product, but also continuously throughout the system’s life cycle. Systecon's analysis of the more than 20-year-old Combat Vehicle 90 is a good example of that.
BAE Systems, which manufactures the Combat Vehicle 90 (CV 90) was asked by the six user nations to conduct a project that from several perspectives analyzed the possibility to equip the vehicle with bands made of rubber. Traditionally, combat vehicles in this weight class are fitted with steel bands, but now it is possible to fit even heavy vehicles with rubber bands that significantly reduce vibration and noise inside the vehicle.
In addition to vibration analysis and fatigue tests of the new rubber components there was a desire to perform an analysis of the consequences in terms of LCC. By outlining how the investment and operational safety of the two options, steel and rubber, affect the LCC, the analysis would provide a basis for a decision. In simple terms, assuming that the combat vehicle would have a certain availability, which of the alternatives, steel or rubber, would be the cheapest during 15 years of operation?
Figure 1. CV 90 with rubber bands. Photo BAE Systems.
Thanks to its knowledge of LCC and access to powerful analytical tools, Systecon was consulted by BAE Systems to join their experts in a comparative LCC analysis to evaluate the impact of replacing the steel band system with rubber on the CV 90.
To perform the analysis Systecon built up a model, an LCC tree, of the cost elements that were relevant when comparing steel and rubber bands. The selection of the costs to be included were made on the basis of what differed between design options. The costs that were the same for both options were not included.
Processing and analysis of data was done in the optimization tool OPUS10® and simulation tool SIMLOX®, while the LCC model and results accumulated and analyzed in the cost analysis program CATLOC®.
Figure 2. An LCC model was built up for the system. The figure shows the top level of the structure. More detail about each part of the structure were subsequently added.
Replacing the steel bands with rubber bands on existing vehicles of course means extra initial costs, but it also creates savings in terms of reduced component failure rates thanks to the reduction of vibrations. This reduction of failure rates affects all the components in the entire vehicle, not just the parts that belong to the existing band system. Reduced vibration also means that the ammunition stored in the vehicle has a longer lifespan and will not be discarded as frequently.
To understand the context in which the analysis was performed, the technical system for the two wagon types (steel and rubber), an operating profile for a certain number of carts, and a supporting maintenance organization were defined.
The LCC analysis showed which of the components or activities were cost drivers, and which design options over 15 years of usage were the most cost effective. It was also possible to see how much the raising or lowering of input conditions, such as component reliability or unit price, affected the final outcome.
Figure 3. The LCC cost of each system is compared. The figure only shows a schematic comparison because the actual costs in the LCC calculation are not public.
As in many other projects, the challenge in working with the LCC model was in getting reliable input data. For the steel bands real operating history and cost data from existing vehicles and contracts were available, but data for the rubber bands needed estimates to some extent due to the fact that they were new products. Thanks to data from manufacturers and BAE Systems' own test activities the model could be completed with the necessary input. Since the input to some extent was uncertain, it was extremely important to carry out sensitivity analyses to be able to form an opinion of how changes in input data and assumptions affect the result.
In the analysis, one problem related to how the indirect costs, or so-called “soft values,” should be handled. One of the major reasons for switching to rubber band is to improve the working environment of the crew. Previously crews have experienced problems with noise and vibration causing physiological damage in the form of white fingers, hearing problems and stress, followed by sick leave. This, however, is difficult to quantify in terms of costs, especially since the damage may be discovered long afterward. If combat vehicles are quieter it also means that the risk of being detected by the enemy decreases, which can change the tactical behavior on the battlefield.
These examples are considered difficult to express in costs in a LCC structure. It can vary from nation to nation; for example, how to value soldiers' safety. The monetary value of a changed tactical behavior is even more difficult to estimate. In the analysis of the CV 90, Systecon and BAE Systems therefore chose to report indirect cost components, but to assign to each user nation the task of quantifying their own costs.
To analyze a change in the design of a system with LCC methodology and reliability parameters is a powerful method to demonstrate how the various design options affect the total cost for the end user. Often, many of the costs or other details are unknown to a new design option, but by analyzing the problem with the data actually available it’s possible to count backwards and come up with the required reliability that the new design must meet to be more cost-effective than the existing one. Sensitivity analysis of relevant data should always be performed to determine how variations in the parameters affect the final result.
LCC analyses performed with Opus Suite identifies and clarifies cost drivers for a system and makes the relationship between reliability, availability and total cost known. It is therefore possible to produce a powerful and flexible analytical model that can quickly generate relevant data, which is useful in all phases of a system's lifecycle. When the cost drivers are known, it is a good starting point for continued efforts to influence the underlying factors.
The analysis of reliability and LCC is of course possible to make more accurate and detailed the better monitoring of the operation of one system.
A recommendation is therefore to decide early which parameters to be measured for each system, and then ensure that it is actually made so that there is structure and quality in the information. In this way, a good basis for working effectively with LCC and Life Cycle Management can be made.