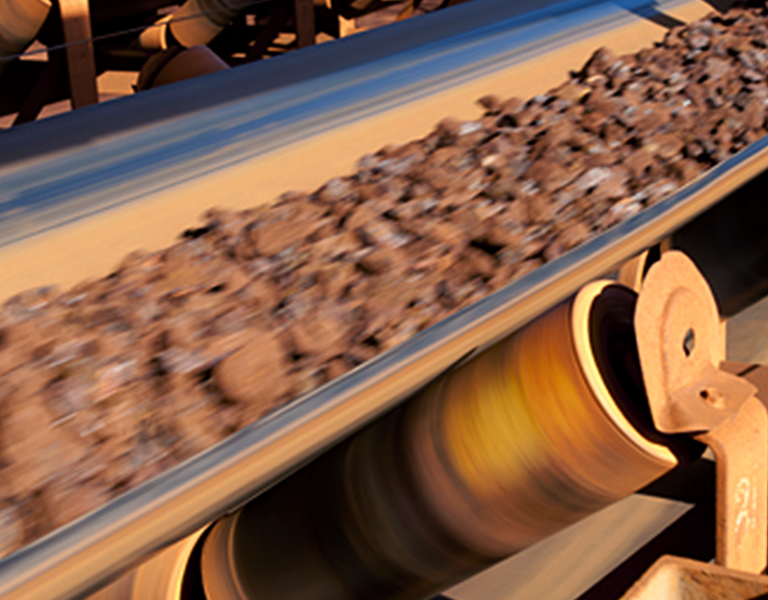
LKAB - Evaluation of Means of Transportation in Mines
The cost-effectiveness of different mine transportation alternatives were evaluated using LCC analysis.
Iron ore has been mined in Kiruna, Sweden since 1890. LKAB's Kiruna iron ore mine is currently the largest underground iron ore mine in the world, producing over 26 million tons of iron ore annually. When the new main haulage level, KUJ1365, was designed Systecon performed LCC analysis to help evaluate the cost effectiveness of different potential ore transport solutions.
Since the mine opened, six main levels have been completed. The ore that was accessible on the sixth main level at 1,045 meters below the peak of the Kiirunavara mountain was expected to become depleted 2017, so the work on designing a new main level at 1,365 meters was begun in 2005.
A new main haulage level entails a significant investment as well as high annual operational and maintenance costs. This means a great opportunity in the early phases to impact the total cost for the level, and increase the profitability. Most of the decisions being made impact both the initial investment and the substantial annual maintenance and operational costs. This means that errors in the early decisions can be very costly if they are not scrutinized and analyzed with an eye towards the total lifetime cost. This also characterizes Systecon's work.
Our role is to look beyond the cost of the initial investment and to calculate, reveal and compare the total lifetime costs for each alternative. The tool used to accomplish this is often called "LCC," Life Cycle Cost. LCC entails breaking down all significant and distinguishing costs for each alternative into their respective components, and calculating each component using mathematical formulas. LCC is also an excellent tool for quick and easy updating of results when new information becomes available, assessing different scenarios under consideration, and performing sensitivity analysis.
In conjunction with designing the new main level, LKAB naturally had to resolve very many questions. One important question was how to handle the horizontal transport of ore from the pockets to the crushers, for subsequent transport to the surface. The existing level at Kiruna used unmanned trains, while LKAB's second major mine in Malmberget used trucks to transport the ore. What were the advantages and disadvantages – in terms of cost effectiveness – of using each of the two transport types at the new main level, and what were the expected lifetime costs?
Systecon participated early on in the design phase by compiling and performing calculations of the lifetime costs of each alternative. The calculations were based on LCC methodology and Systecon's proprietary LCC tool, CATLOC.
Systecon participated in the pre-design work by creating and compiling a parameterized cost model that took into account the construction of the new level, vehicle procurement, vehicle operation, site and vehicle maintenance, personnel costs, etc. Using this model, the two alternatives could be compared to each other using alternative scenarios and sensitivity analysis. The original purpose of the analysis was to determine which of the two main alternatives, rail or truck transport, was the most cost effective and what the cost drivers were for each alternative. A hybrid rail and conveyor belt alternative was added at a later stage. The results of the analysis showed very clearly the cost advantages of a pure rail alternative. The sensitivity analysis also showed that the results would not change even if the parameters were altered significantly in favor of the truck alternative.
The results of these calculations constituted very useful data for deliberations and decisions but also raised many different kinds of questions. All the questions could be answered quickly and easily – often in the course of the ongoing meeting – by quickly running the model using the new specifications.
On October 28, 2008, LKAB's Board of Directors decided to construct the new main level at 1,365 meter, and to implement horizontal transport using remote-control rail haulage.
Quote by Hans Engberg, General Manager, Projects, LKAB:
Systecon's systematic work methods, skilled staff and effective software have been critically important when deciding on the final design of the new underground transportation system in the Kiruna mine, KUJ 1365. Because of Systecon's expert handling of our many interacting, interdependent plant components and steering parameters, it has been exceptionally satisfying to be able to address new issues during the evaluation of the different alternatives in an objective and factual manner.