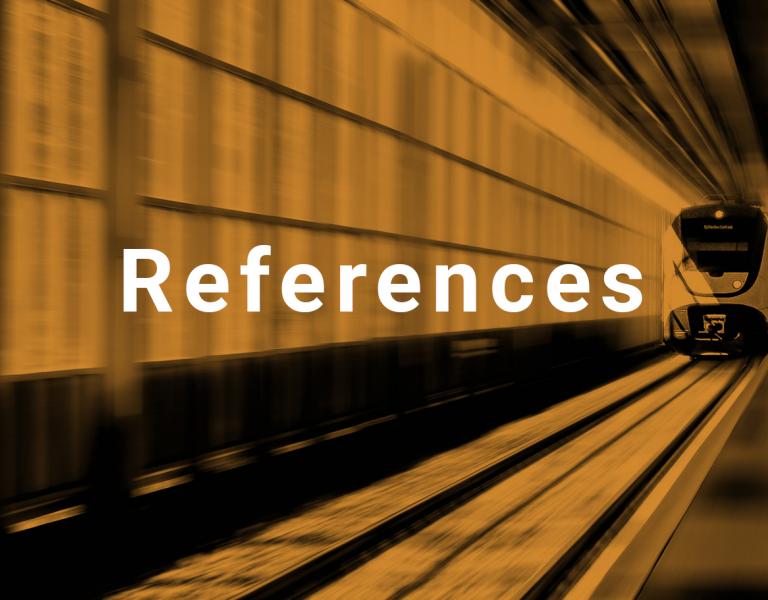
Öresundståg - Analysis for dimensioning of high-cost components inventory
Optimization of high-cost components to create maximum availability for the rolling stock.
Öresundstågen is the regional and commuter train network that stretches from southern Sweden to Helsingör in northern Denmark via the Öresund bridge. Since the service started in 2000 the fleet size has gradually expanded. Today there are 109 trains. In addition, the stock of high cost components (HCC) has been expanded over the years and the rolling stock managers needed to ensure that the stock is correctly dimensioned. Utilizing the optimization tool OPUS10, Systecon was able to identify deficiencies and propose more cost-effective solutions to reduce the expected waiting time for HCC.
HCC are characterized by high costs and long lead times. At intervals defined in the maintenance plan, HCC are replaced by spares from an HCC inventory. A single replaced component is then overhauled and reprocessed at a workshop before it is put back in the inventory to be used in an upcoming replacement. If there are not enough of these components and the overhaul time is long, there is a risk of shortages. The mean waiting time or, in other words, the average time that a planned replacement task has to wait for a spare part is a suitable parameter to optimize in order to increase the cost-effectiveness of an HCC inventory
Together with the responsible rolling stock managers from Transitio, DSB and Öresundståg, Systecon compiled the necessary data for the HCC included in the analysis. The data included prices, failure rates, replacement, repair- and reprocessing times and the maintenance plan. A model, made in Systecon’s optimization tool OPUS10, was used to analyze the existing stock of high-value components for the trains.
The analysis showed that most of the HCC have a high availability while a few of them have a moderate risk of shortage. Based on this result, Systecon proposed three concrete measures to increase cost-effectiveness; in other words, ensuring the highest possible uptime and lowest possible cost.
1. Acquiring new HCC according to priority
A priority list for the acquisition of HCC that specifies the specific purchase that provides the most cost-effective reduction of the mean waiting time for the components. The figure below shows how the mean waiting time decreases when purchasing new components. The existing stock corresponds to the uppermost point with the highest mean waiting time. The next point on the curve corresponds to the acquisition of the HCC that reduces the mean waiting time most cost-effectively. The following point corresponds to the next optimal acquisition etc. This provides clear decision support for rolling stock managers when considering investing in new high-cost components to reduce the risk of shortage.
2. Optimizing reprocessing times
An alternative to acquiring new HCC could be to reduce the reprocessing times of the replaced components. For those HCC that are in plentiful supply it could be more cost-effective to allow an increased, and most likely cheaper, reprocessing time. Thus, rolling stock managers have obtained documentation showing what room there is to negotiate reprocessing times with the supplier.
3. Balancing the maintenance to reduce demand bulges
Each component of HCC stock should be dimensioned according to the most intense period of maintenance. The need for these components could be reduced either by moving forward some of the preventive maintenance tasks or by using condition-based maintenance for these components.
The OPUS10 analysis is a good example of how optimization of HCC results in a number of actions that can be taken in terms of inventory and reprocessing times, with the overall aim of achieving maximum availability of the rolling stock at the lowest possible cost.