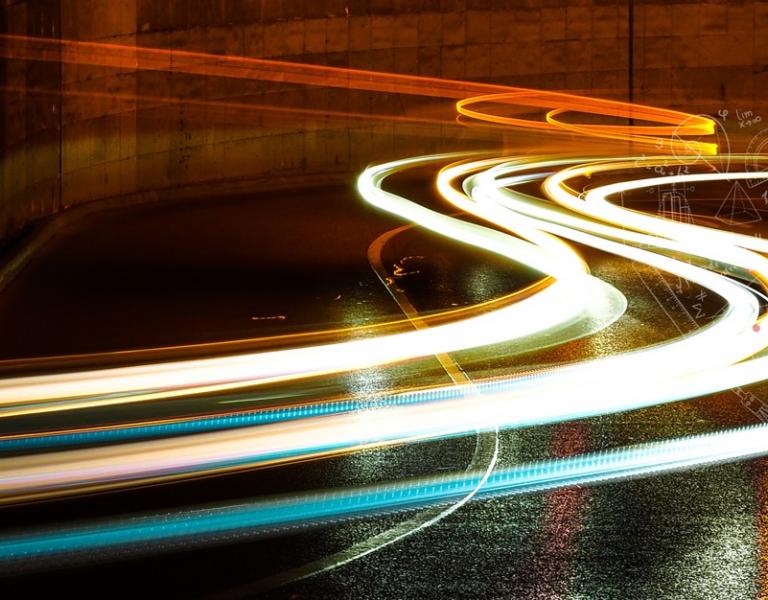
Holistic Fleet Management vs Inventory Optimization
Inventory Optimization Challenges
Managing spare parts inventories for military equipment is challenging. Spare parts demand is driven by maintenance philosophy but predicting when and how often those needs will occur has traditionally been difficult because spares forecasting, maintenance planning, system configuration management, and systems operation were accomplished by disparate groups using disparate tools in unique silos.
Most complex systems are maintained in a turbulent environment, driven by unpredictable human decisions that drive budget crises, wars, reset, maintenance programs driven by system and part criticality and mission requirements, operating tempo, deployment, and a host of other factors. OEMs, manufacturers and vendors see orders for new stock or repaired items as unpredictable and erratic. It isn’t steady business, so suppliers work these items into production at their convenience. This result is inconsistent lead times or significant excess inventories, both of which are inefficient and do not enable cost-effective war fighter capability.
Assumptions & Supply Chain Planning
When teams modernize inventory planning systems, they assume that replacing old systems, without also better integrating business processes, and understanding the root causes of demands and maintenance will drive improved business results. Many companies offer “next-gen improved inventory management solutions,” but while the pitch may be intriguing, it’s missing the forest from the trees. Inventory planning is but one small aspect that drives mission capability. Even the best inventory planning systems are built on assumptions, with limited insights into configuration, utilization, and maintenance. Assumptions are often wrong, and so are the results.
Enter the Common Readiness Model for tactical and strategic optimization. Systecon has spent years developing integrations with major PLM systems including Windchill, Team Center, EAGLE and others that are compliant with GEIA-0007 and S3000L and mission planning systems to automatically link to detailed system product structures to understand configuration, redundancy, mission criticality, and maintenance philosophy.
So-called "next generation" inventory planning and inventory management solutions operating in a narrow silo would apply a risk-based approach to an apparent lumpy or unpredictable demand pattern. An example of this approach in action is missile defense radar transmit/receive modules. Because of component redundancy, infrequent utilization, and maintenance philosophy, demands appear to be “impossible to predict.” This is a fallacy oft repeated by sales executives at inventory planning software companies that simply lack the integration points to understand that by maintenance policy, the radar system is only maintained when it reaches a critical level of redundancy degradation, and based on operating tempo would only be maintained once every 3-5 years. The inventory-only approach would see 200-300 transmit-receive module demands in the supply system all at once, every 3-5 years as a very infrequent, irregular pattern. Comprehensive fleet management with Opus Suite tie to maintenance and operations systems to accurately align stockage strategy to mission capability requirements, automatically adjusting as operational plans change using revolutionary heuristics, optimization techniques, and simulation to ensure the right part in the right place to maximize mission capability at the lowest possible cost. With Opus Suite this apparent infrequent and irregular demand is quite predictable and expected. With Opus Suite you can not only predict the unpredictable but phase the buy in over time using advanced simulation and optimization techniques to avoid the “steady state” trap of many statistical models.
Proven Performance & Validated Algorithms
Proven with the United States Navy on a multitude of programs including AN/SLQ 32 and AN/SPY-6, Opus Suite reduced spare parts inventory by more than $200M on AN/SPY-6 alone and more than $5B across the US DoD. This proven performance, independently validated and verified algorithms, and ease of use by Government personnel have led to a US Navy mandate to use Opus Suite and the selection of Opus Suite by the F-35 program, NAVSEA, NAVAIR and others to optimize, simulate, and quantify risk in weapon system performance after a comprehensive industry evaluation.
Stop viewing inventory transaction through a straw and expand your vision. Contact Systecon today to learn more about our approach to comprehensive fleet management with Opus Suite and enable your organization to predict the unpredictable.